Additive manufacturing
The additive manufacturing term refers to all Production method, in which material layer is applied to a three-dimensional component for layer. The forming method has its strengths, especially in highly complex structures, and enables the user to have a high degree of design freedom and functional optimization.
To date, additive manufacturing has been used predominantly in prototype construction and in the production of small batch sizes. Meanwhile, however, the technology is increasingly moving into series production, as it enables the strong individualization of products and gives the user the opportunity to differentiate themselves on the market.
Technical Basics for Additive Manufacturing
Additive manufacturing is based on the layer-by-layer application of material. For this reason, the technology is also referred to as layer-based technology. The process of the production method always begins with the imaging of the desired component contour in a three-dimensional CAD data set. In the engineering phase, this can optionally be generated by means of conventional CAD construction, by scanning or by other imaging methods such as computer tomography (CT scanning).
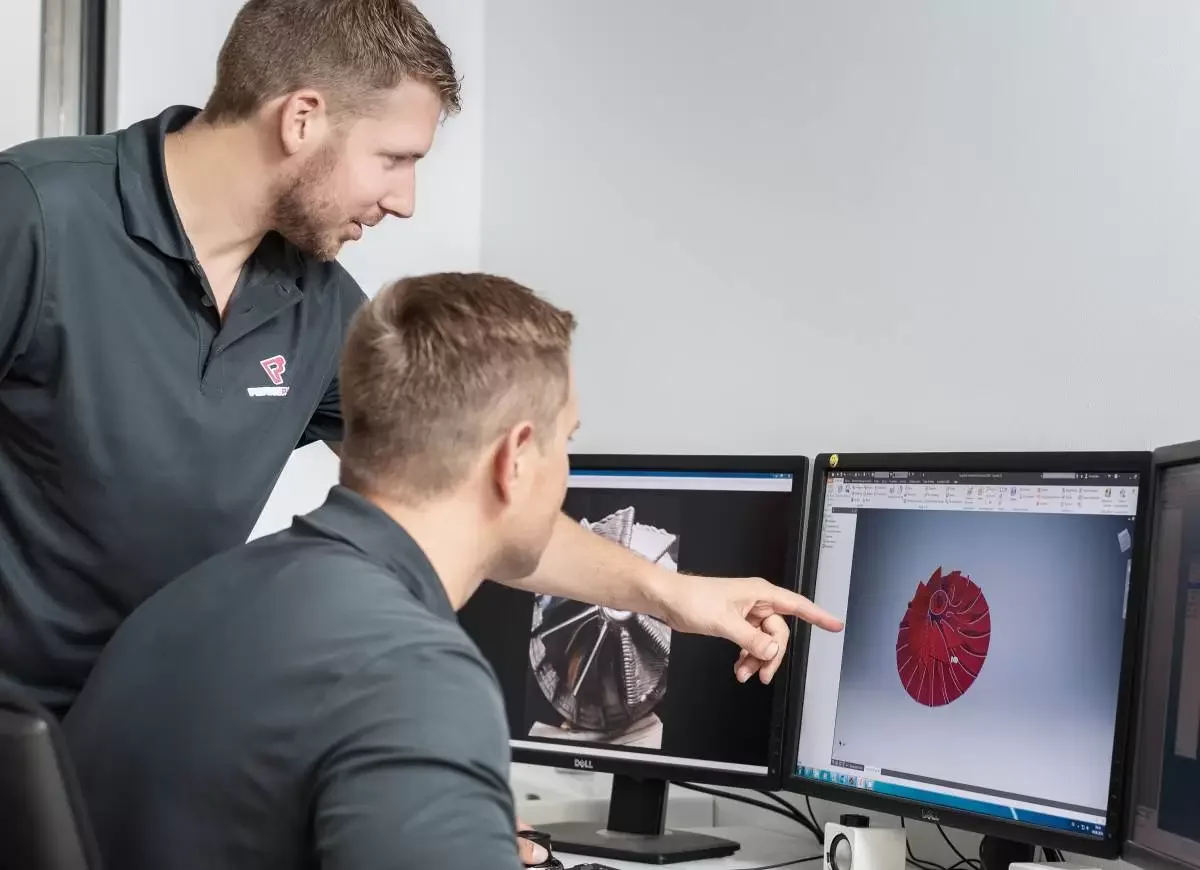
Additive Manufacturing: CAD Construction of the company Flying Parts GmbH
In the second step, the CAD dataset is sliced into layers using specialized software. Each layer typically has the same thickness. The resulting dataset contains the necessary contour data for each layer in the two-dimensional plane, as well as the layer thickness.
The CAD data of the component are then read into a 3D printer. The actual printing process then differs as a function of the process variant. In selective laser melting, for example, the material to be processed is first applied in powder form to the building platform as a thin layer and then melted by a strong laser beam according to the construction data. The second powder layer is then applied and is connected to the layer lying underneath by renewed melting. After each step, the construction platform is lowered by the layer thickness. In this way, the desired component is produced step by step.
-der-Firma-H+E-Produktentwicklung-GmbH.webp)
Support structure - Selective laser melting (SLM) from H+E Produktentwicklung GmbH
In what cases is additive manufacturing useful?
Additive manufacturing processes are predominantly used in areas in which small numbers of pieces with complicated geometric contours and a high degree of individualization are required. In the early years, additive manufacturing was mainly used for the economical and efficient production of prototypes and is therefore also called rapid prototyping. In the course of development, however, the method was also more and more interesting for the production of tools (rapid tooling) and the production of components (rapid manufacturing) in small quantities.
Whether a conventional method, such as injection molding or milling, is used or additive manufacturing is economically sensible depends primarily on the material and the number of pieces.
The following table compares the 3D printing with conventional manufacturing methods and shows when the additive manufacturing represents:
Technology | Number of pieces | Materials |
---|---|---|
Injection moulding | 1 – 1,000 | Thermoplastic plastics |
Die casting | 1 – 1000 | Aluminium, Titanium, Nickel alloys |
Milling (CNC) | 1 – 50 | Stainless steel, tool steel, aluminum, titanium, nickel alloy |
Compared with injection molding and die casting, additive manufacturing has the advantage that the expensive production of molds/tools and their changes in the manufacturing process are eliminated. Compared with the material-removing methods such as milling, the 3D printing has the advantage that the additional working steps after the original molding are largely eliminated.
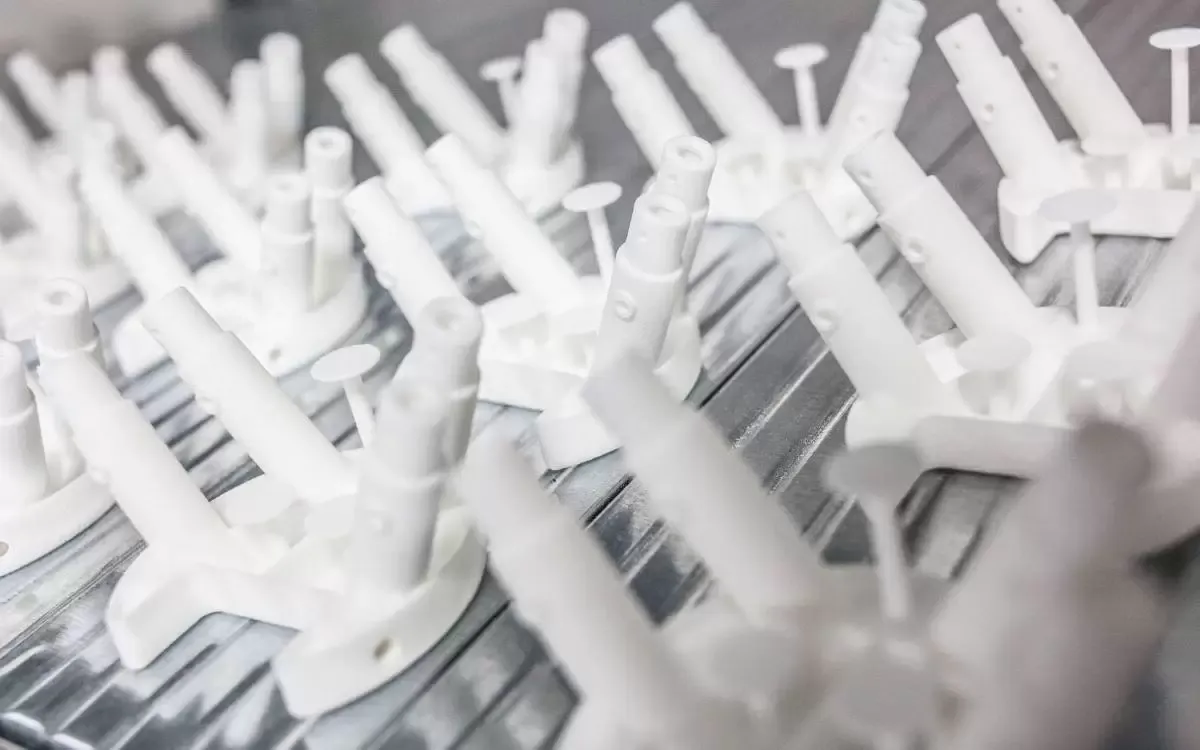
Additive Manufacturing: Drones from Materialise GmbH
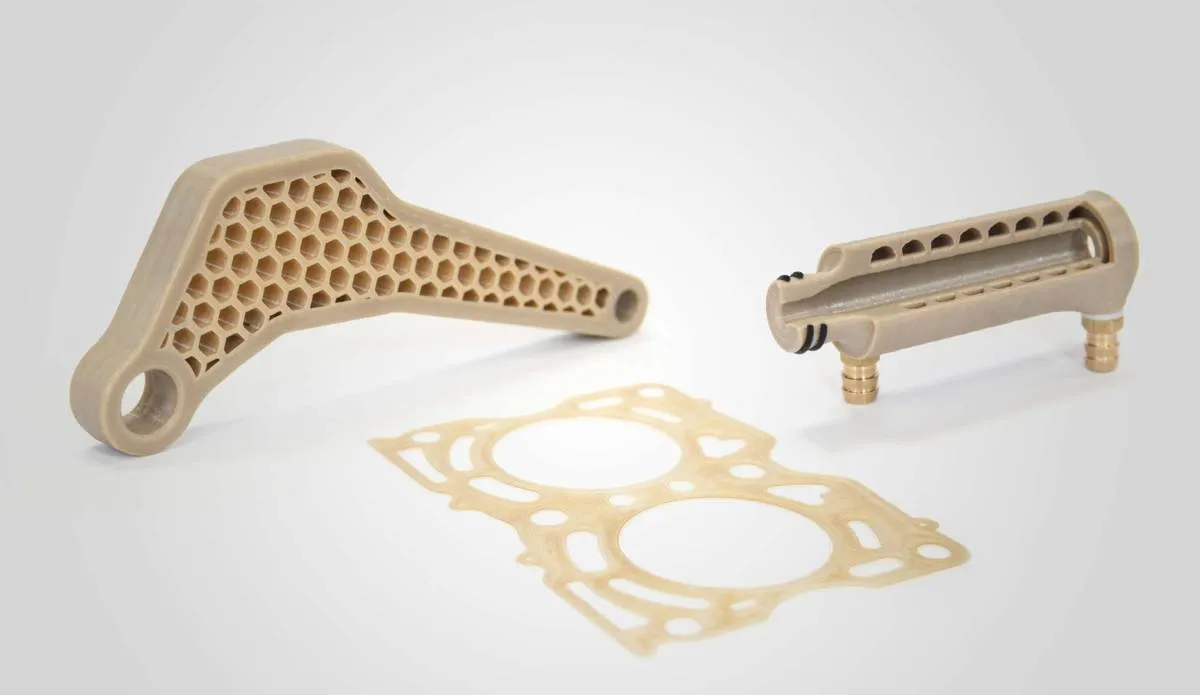
Additively manufactured PEEK parts from Dipl.-Ing. Brecht GmbH
Which materials can be used?
A large number of materials are now suitable for additive manufacturing. These include:
Plastics:
- Polyamide
- HIPS
- PHA
- PEEK
Metals:
- Aluminium
- Steel
- brass
- Titanium
- Gold
- Silver
Other substances:
- Gips
- Ceramics
- silicone
- Art waxes
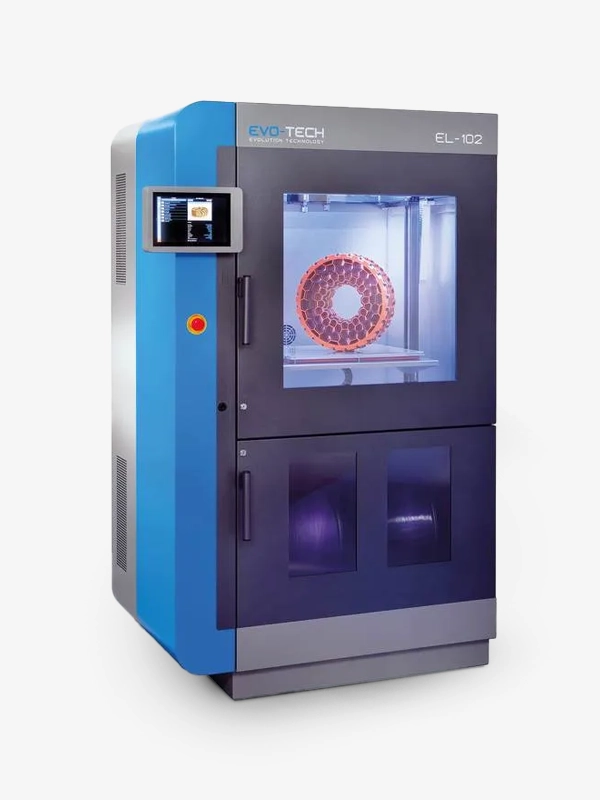
Fused-Deposition-Modelling plant of PMT GmbH
Which variants are there?
Some important additive manufacturing processes, the respective functional principle and the materials used are explained in the following table:
Processes | Abk. | Principle | Materials |
---|---|---|---|
Stereolithography | SL | UV laser selectively cures a UV-sensitive liquid resin corresponding to a product cross section. | Photopolymers, acrylates, epoxys |
Binder Jetting | 3D-P | Binder is printed by push button in powder substrate, whereby the particles are glued together. | Powdered plastics, metals, ceramics |
Selective laser sintering | SLS | High-energy laser beam locally melts powder particles according to component contour. | Part-crystalline thermoplastics |
Selective laser melting | SLM | High-energy laser beam locally melts powder particles according to component contour. | Weldable metal powder |
Wax pressure method | PJM | Wax is melted, guided by a push button, placed on the component plate and cures there. | |
Stranding method | FDM | Plastic filaments are passed through a heated nozzle and then glue in the heated state. | Amorphous thermoplastics |
Inkjet UV printing | MJP | UV-curing prepolymers are deposited in a spatially resolved manner and cured by UV lamp. | Photopolymers, acrylates, epoxys |
Electron beam melting | EBM | Electron beam melts powder particles locally. | Metal powder (mainly titanium) |
Direct metal powder spraying | DMD | Metal powder jet is welded in the focus of a laser spatially resolved. | Weldable metal powder |
3D Metal Print/wire application welding | 3DMP | In wire application welding a wire withte laser beam is melted onto the base material. | Welding wire |
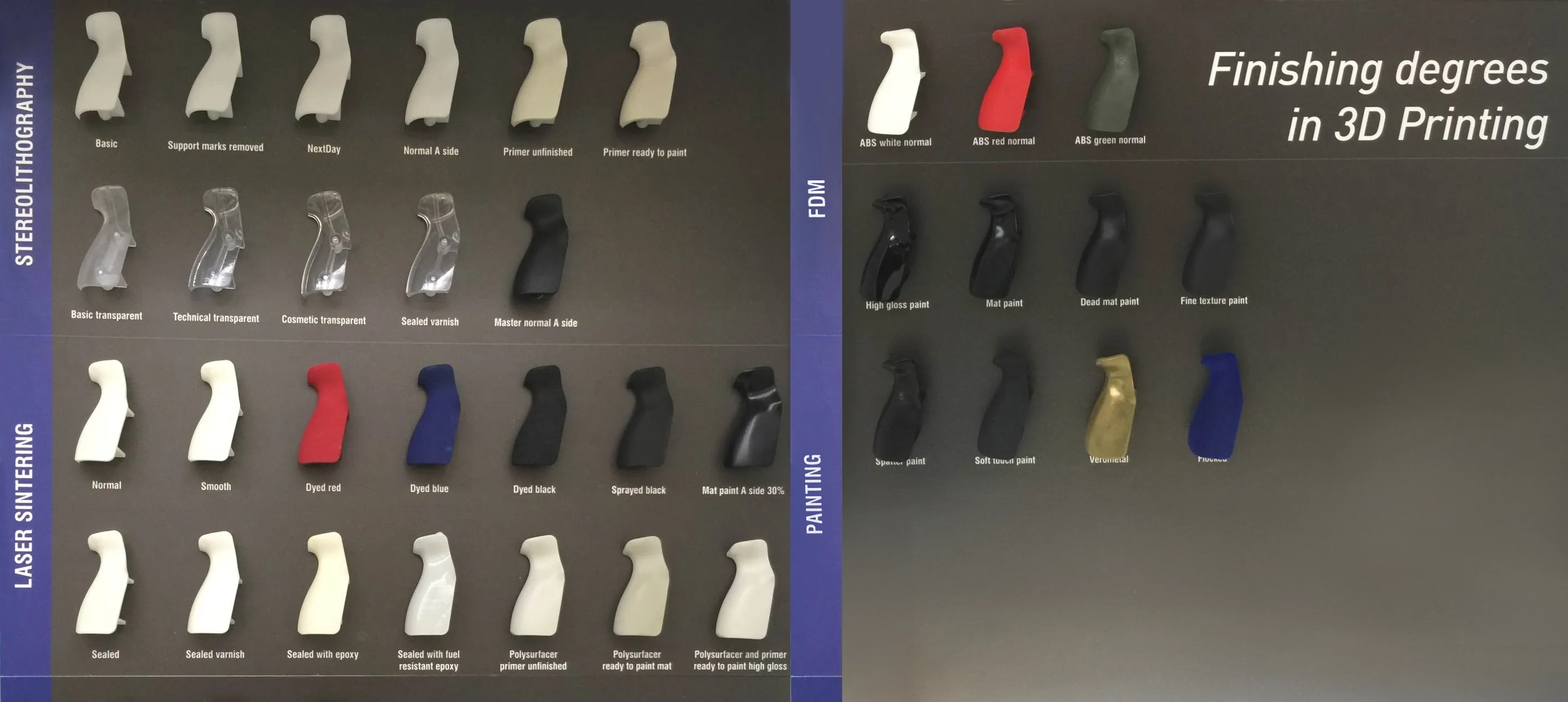
Overview of additive manufacturing methods by Materialise GmbH
Find companies for additive manufacturing
If you are looking for an additive manufacturing company, Techpilot will find numerous companies specializing in this field. Techpilot – Europe's largest platform for orders from drawing parts – provides an application to bring buyers and suppliers together. Making valuable contacts, finding suitable companies for specific orders or writing out online – the portal offers a variety of possibilities. The Techpilot team consists of technically trained experts who are happy to help you by phone, email or chat. The service staff advises you on the use of Techpilot and gives you tips on how to quickly and easily find suitable suppliers or write out inquiries.
Examples of jobs in the Techpilot marketplace
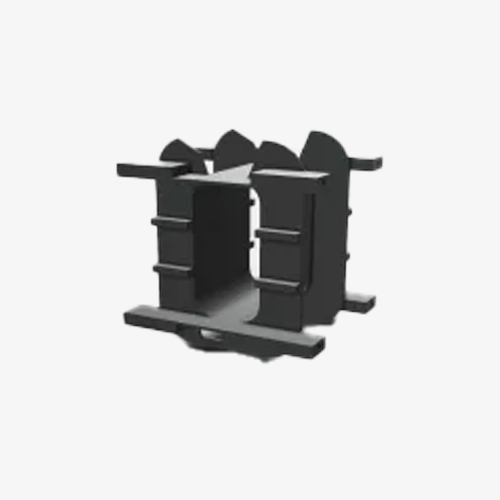
Coil body - additive manufacturing

Aluminium part - Selective laser sintering

Multi-use tray made of thermoplastics - 3D printing
More about additive manufacturing
Techpilot is Europe’s largest platform for the manufacturing industry.
For over 25 years, we’ve been connecting buyers, suppliers, and manufacturers that are the perfect match – enabling accurate price discovery for custom-made parts. Covering the full spectrum of mechanical components and supporting more than 280 manufacturing technologies, Techpilot is the market leader in Europe.Buyers gain instant access to qualified suppliers, full market transparency, and increased efficiency in their e-sourcing processes.
Suppliers benefit from high online visibility, extended media reach, and a profitable digital sales channel through Techpilot.
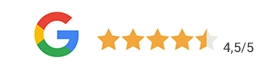
Lexicon Themes
- Metalworking (31)
- Plastic processing (8)
- Parts (8)
- Surface treatment (8)
- Welding (7)
- Machining (6)
- Sheet metal processing (6)
- Cutting (6)
- Turning (5)
- Manufacturing (5)
- Milling (4)
- Tool making (4)
- Suppliers (4)
- Casting (4)
- Procurement (4)
- Contract manufacturing (3)
- Profiles (3)
- Automation technology (2)
- Gearing & Thread (1)
- Forging (1)
- Wire processing (1)
- Heat treatment (1)