Drop forging
The forging is part of the group of forming methods. In industry, it is mainly used for the automated production of metal components that are subject to dynamic loads. The use of at least two shaping tools, or sinks, which move relative to one another is characteristic of the method.
Forming by means of sinks is the most widely used forging method in industrial practice. The method is distinguished by the good material utilization, the die forging parts by the advantageous ratio between weight and strength. From the likewise widespread free-form forgings, the method is distinguished by the superior dimension accuracy.
As a hot-massive forming method, the die forging is based on the fact that the dies have an effect on the metallic material and thus push it in a specific direction. In this way, the material receives the geometry imaged in the sinks as negative. These cavities in the sinks are called engravings. The forming temperature during forging is usually above the austenitization temperature of the material. In process variants, however, the starting blanks are also processed at room temperature or just below the recrystallization temperature. Although blanks made of sheet metal can be used, because they are also reshaped into three-dimensional bodies, a solid forming process is called for when forging.
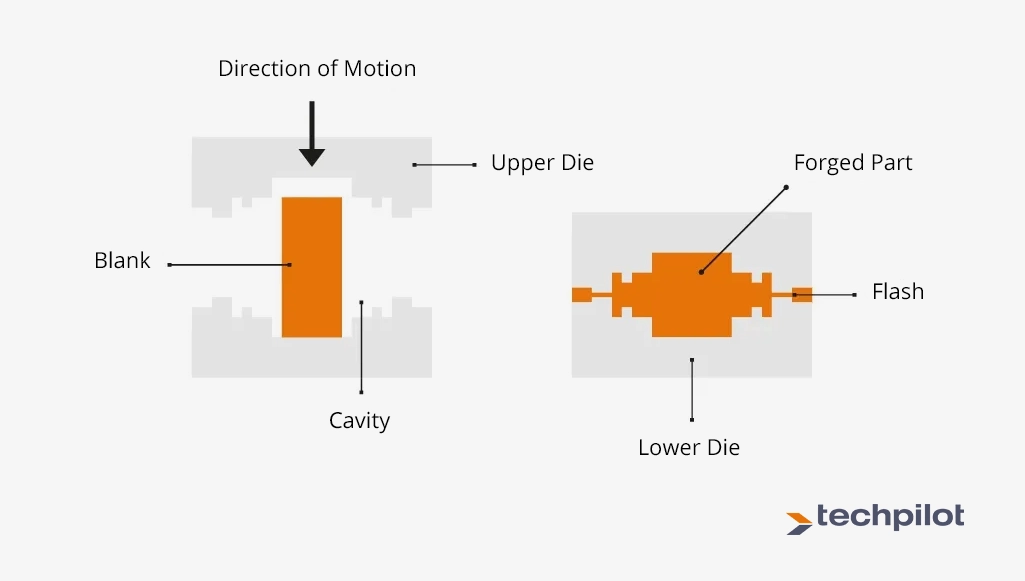
Gesenkschmiede process
The typical procedure can be divided into the following phases:
1. Heating
Using different heating systems, the blank is heated to the required forming temperature.
2. Formation
This step is not always necessary. Here, the mass distribution of the raw part is approached to the final shape by means of free-form forging.
3. Forging
The workpiece is now in the die, where as a rule several strokes or impacts of forging press or hammer perform the actual deformation.
4. Deburring and Holing
This step serves to remove excess material which exits along the burr gap between the sinks. If it requires the workpiece geometry, such as for example in a Plug, the forging part is additionally perforated.
5. Subforms
The pressing can take place on the cold and on the warm raw part and achieves an increase in the geometrical accuracy.
6. Heat treatment or heat treatment
In this step, the forging part receives a thermal treatment for the purposeful adjustment of the material properties.
7. Descaling
Here, residues from the previous processing are removed from the forging part.
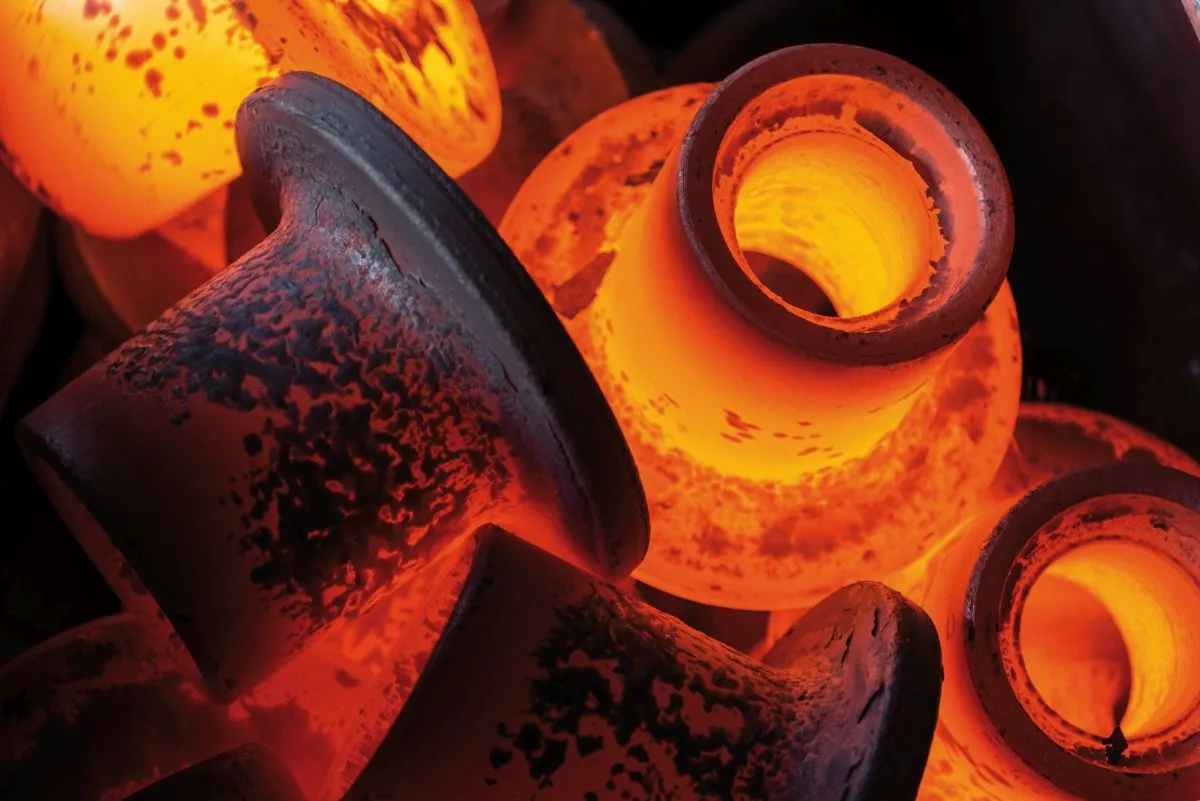
Gesenkschmiede - Parts of ISEF STEEL FORGINGS Srl
Use of die forging
As a highly productive Production method for the production of complex components, the die-forging has a special significance in industrial production. In addition to the high degree of utilization of the feed material, the structure typical of forging is responsible for this. The fiber course follows the shape of the component, which ensures a high strength. The process of the mostly highly automated forming process is characterized by short process cycles.
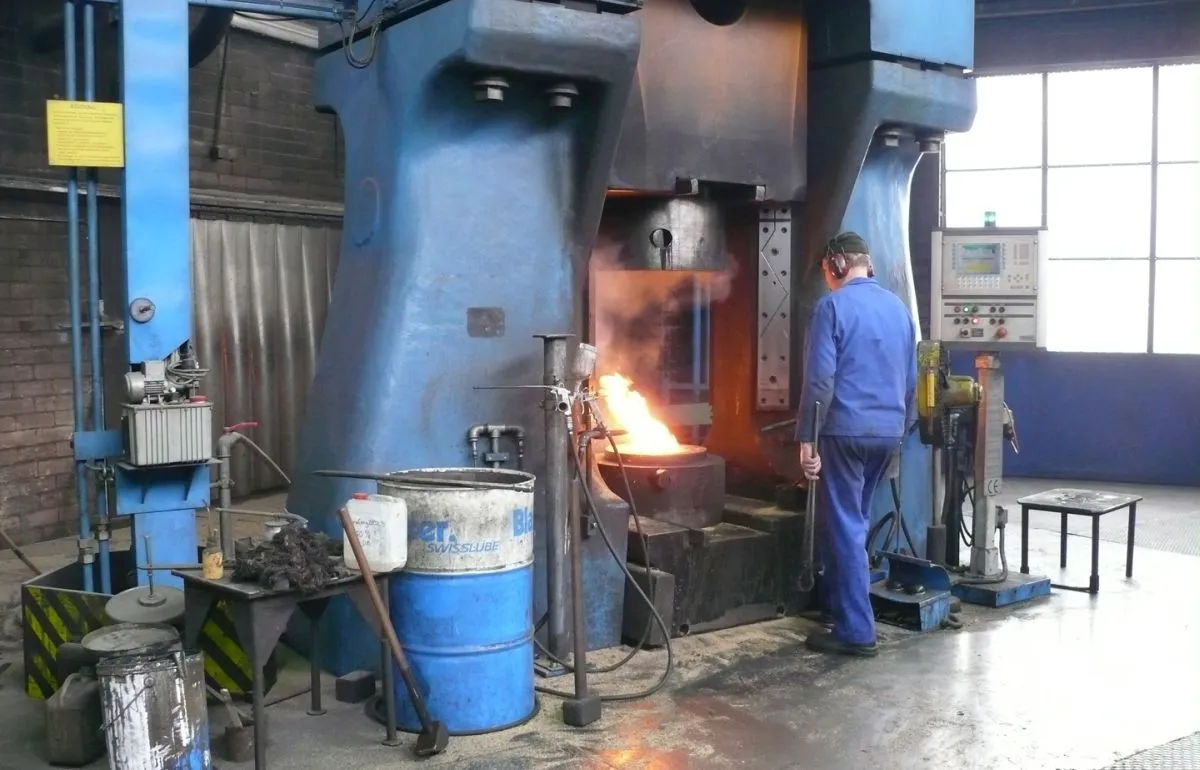
Gesenkschmiedehammer from Flükiger & Co AG
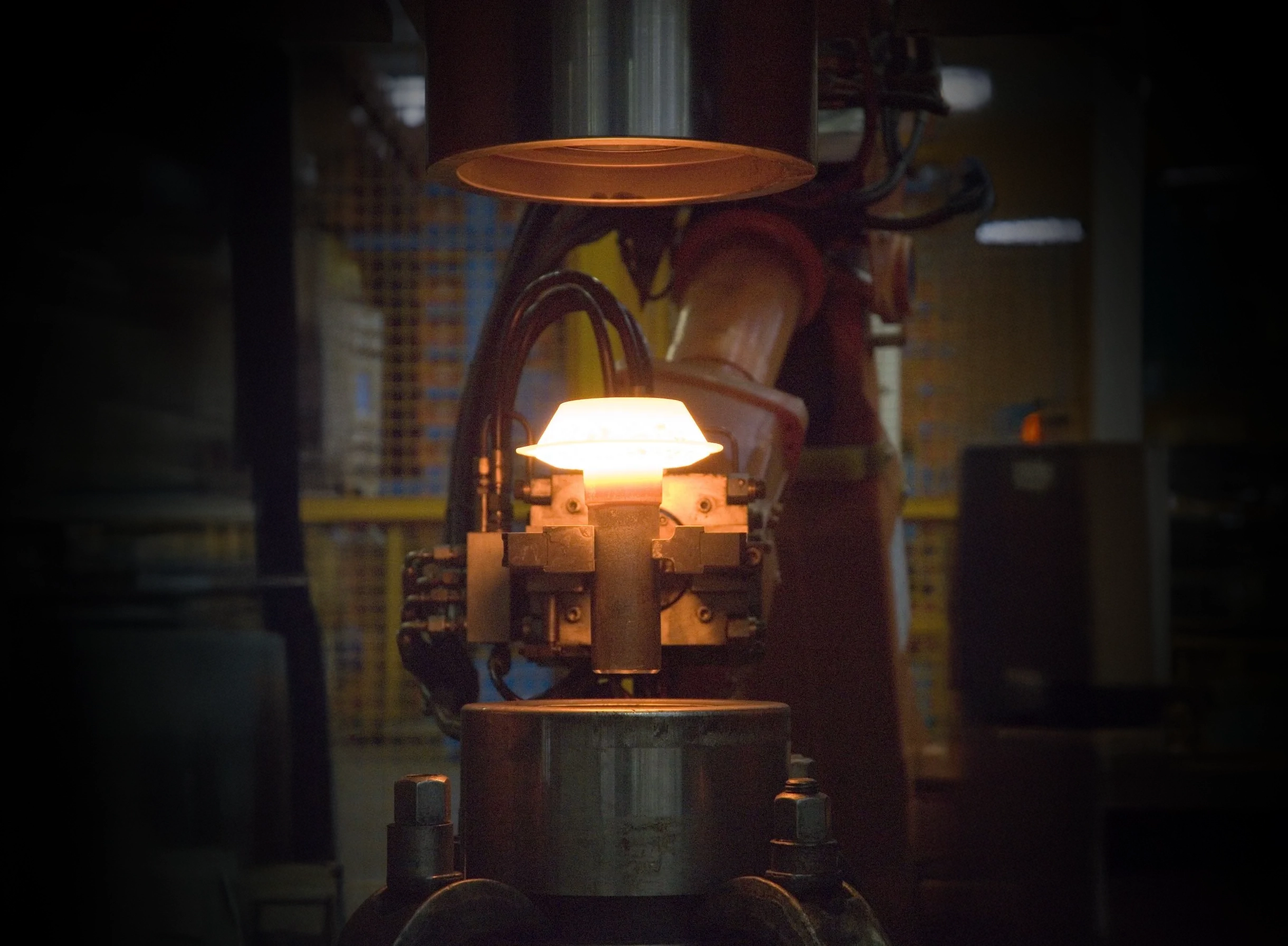
Forging - Company Poppi Ugo Euroforge S.p.A.
The main customers for die forging products are in sectors where weight-optimized components are subject to high dynamic loads:
- Automotive industry
- Two-wheeled industry
- Mechanical engineering
- Railway industry
- Shipbuilding
- Aircraft construction
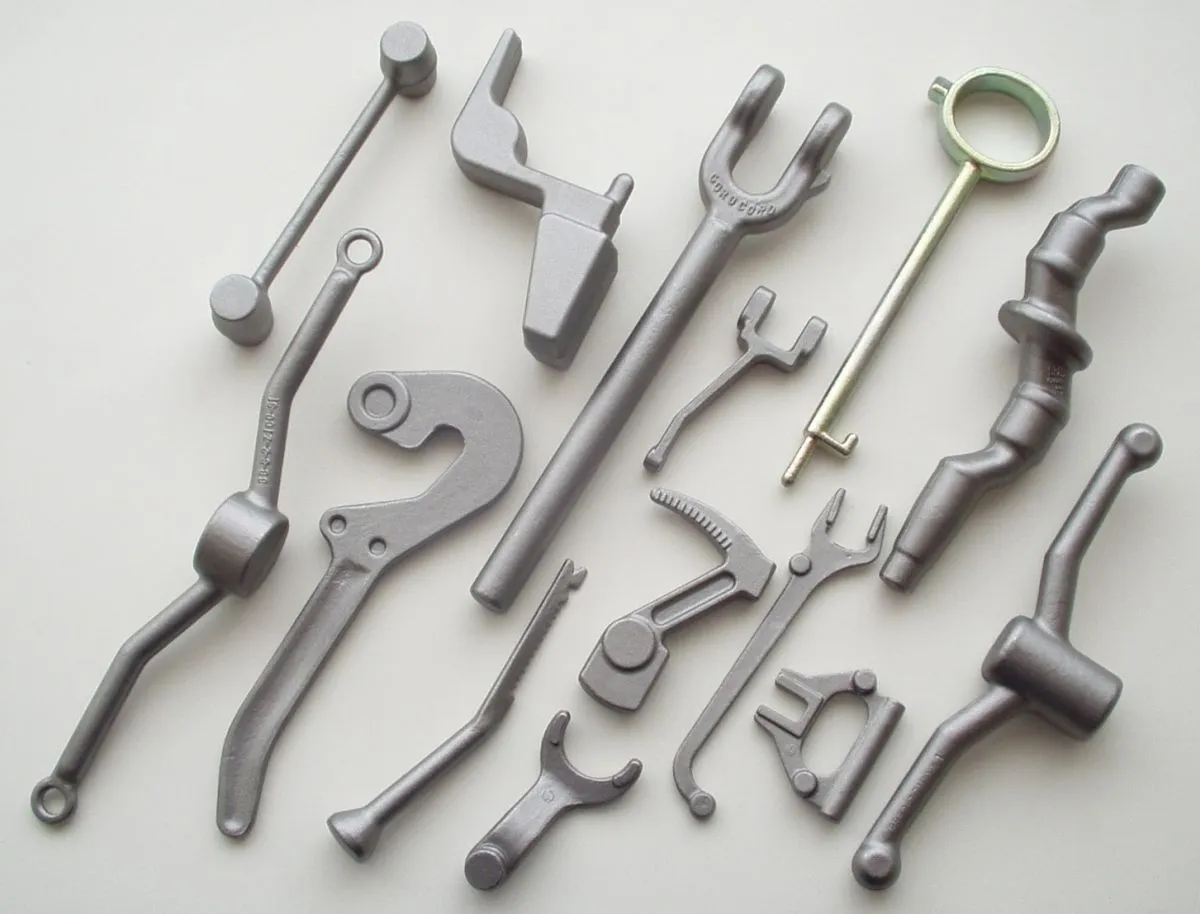
Gesenkschmiedeteile GmbH
Drop forging is associated with increased effort for tool creation and high investment in automatic forging systems. For large-scale production, the less energy-intensive variant of die forging has prevailed as semi-hot forming. It allows a better structure and narrower manufacturing tolerances. In addition, a process variant is available for applications with extended requirements for dimensional accuracy: In the case of precision forging, it is often possible to dispense with a cutting aftermath.
Materials for forging
All metals which can be kneaded after their heating are suitable in principle for forging. These include the following non-ferrous metals and steels, including alloys:
- Steel
- Stainless steel
- Magnesium
- Copper
- brass
- Aluminium

Aluminium forging parts for motorcycle construction, after-treated, company Mark`skill Enterprise Co., Ltd.
In addition, special nickel-based and titanium alloys are increasingly used. The advance development of special materials with pronounced reshaping capacity for hot mass forming promises the shortening of the production chains and thus the increase in productivity. On the technical side, special lightweight materials and hybrid material composites as well as process parameters adapted thereto permit an even better ratio between strength and weight of the components.
Find companies for Drop forging
If you are looking for a supplier specializing in technology Drop Forging you will find a wide range of suitable companies in Europe's largest drawing database. Techpilot offers a platform for networking and building new business relationships for buyers and suppliers. The search function offers a wide range of filtering options to find exactly suitable plants for the required parts.
Buyers use all Techpilot functions for free. In addition to the supplier pool, this also includes the function of the application with which requests for drawing parts can be uploaded. Interested companies send specific offers that can be clearly managed and quickly compared with each other.
The Techpilot team consists of technically trained experts who help you to use the platform. Do you want to know more about Techpilot? We offer you free advice.
Examples of jobs in the Techpilot marketplace
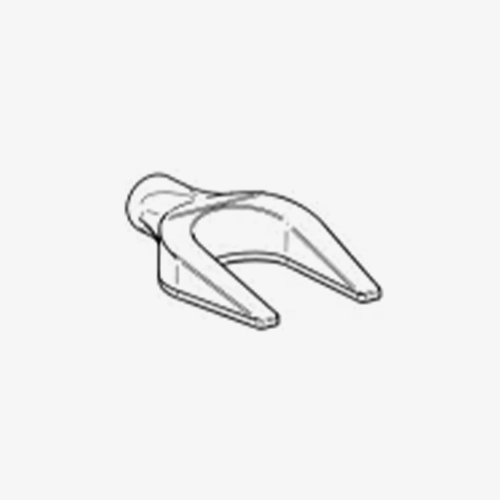
Request for Gesenkschmiede - Fork
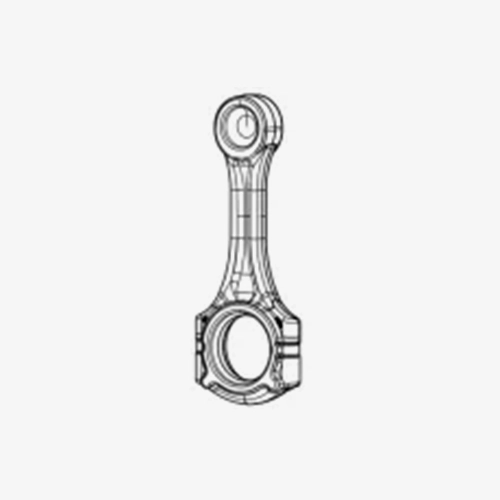
Request for Gesenkschmiede - Pleuel
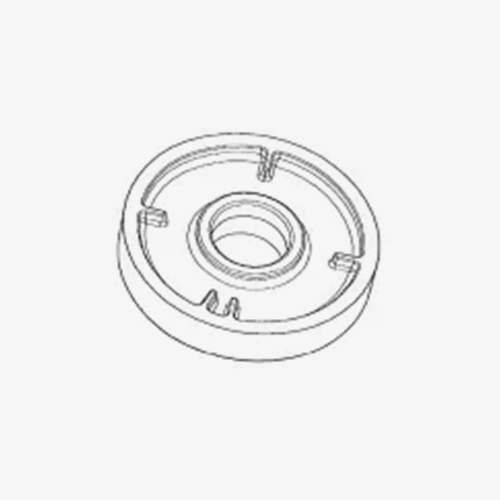
Request Gesenkschmiederohlinge
More about Drop forging
Find companies for
Techpilot is Europe’s largest platform for the manufacturing industry.
For over 25 years, we’ve been connecting buyers, suppliers, and manufacturers that are the perfect match – enabling accurate price discovery for custom-made parts. Covering the full spectrum of mechanical components and supporting more than 280 manufacturing technologies, Techpilot is the market leader in Europe.Buyers gain instant access to qualified suppliers, full market transparency, and increased efficiency in their e-sourcing processes.
Suppliers benefit from high online visibility, extended media reach, and a profitable digital sales channel through Techpilot.
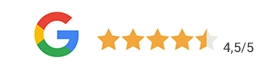
Lexicon Themes
- Metalworking (31)
- Plastic processing (8)
- Parts (8)
- Surface treatment (8)
- Welding (7)
- Machining (6)
- Sheet metal processing (6)
- Cutting (6)
- Turning (5)
- Manufacturing (5)
- Milling (4)
- Tool making (4)
- Suppliers (4)
- Casting (4)
- Procurement (4)
- Contract manufacturing (3)
- Profiles (3)
- Automation technology (2)
- Gearing & Thread (1)
- Forging (1)
- Wire processing (1)
- Heat treatment (1)