Gravity casting moulds
A mold is a metallic mold used for the production of precise workpieces with good surface quality. Moulds often consist of cast iron or copper plates and are widely used in metalworking industry.
The mold is the technical basis of the mold casting process and has proved successful in the production of large forging blanks, slabs for sheet metal products, billets for wire, rod and profile products and other components. In the mold casting process, the metallic melt is poured into the mold via the above-lying injection and cures there. Depending on the casting process, a mold can be used up to 100,000 times, resulting in a high cost.
What is a mould?
The mold gives the casting part its later shape within the mold casting process and usually consists of cast iron or steel. The production costs for a permanent mould are very high, which is why the production of a mould is exclusively for series production. The investment in the development and production of the mould is often only profitable after a number of thousand castings.
-Co.,-Ltd..webp)
Glass of Sky-tech Manufacturing (Ningbo) Co., Ltd.
When producing a mold, it is important to use high-quality, temperature-resistant steel. The key requirements for the mold include:
- Sufficiently high melting point
- Resistance to high temperatures
- Resistance to rapid temperature changes
- Resistance to wear
- High mechanical strength
- Low thermal expansion
- Good thermal conductivity
- Tempering resistance
Although moulds are permanent moulds suitable for several thousand inserts, they nevertheless have a maintenance requirement. Thus, the protective finishing – this is a layer of graphite and quartz flour – has to be renewed again and again after several castings. This prevents the melt and the mold from welding. In addition, the size prevents abrasion from the mold and regulates the cooling effect.
Which variants of molds are there?
In the case of molds, a distinction is made primarily between die casting molds and die casting molds. Molds for block casting are characterized by simple geometric contours and are suitable for producing large components with high weights. Typically, molds for the block casting can be seen on their conically beveled sides. The conicity facilitates the release of the casting after solidification of the material.
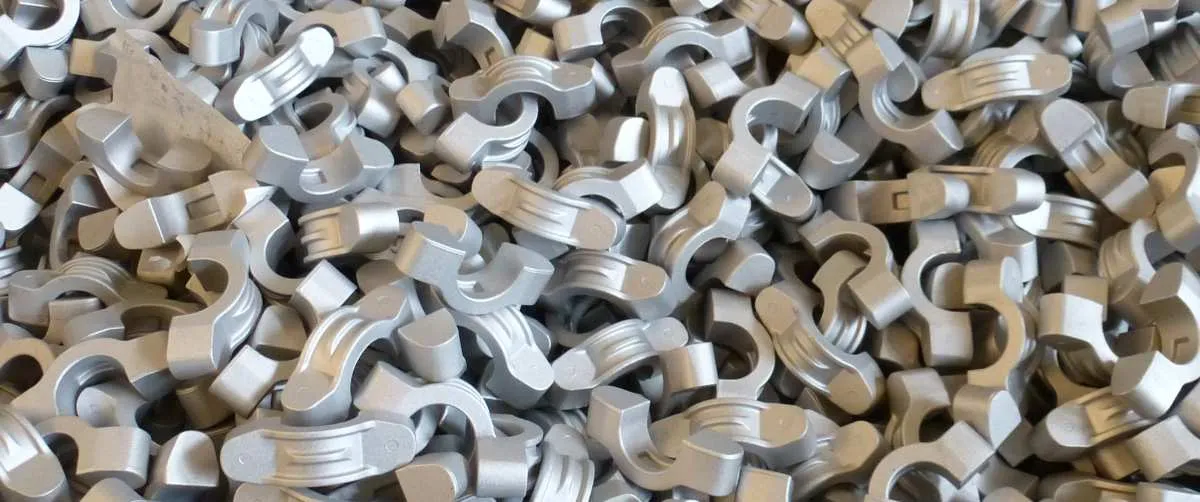
Alu mould casting from Glenck Bischof AG
In block casting, it is important to avoid sharp corners on the mold. If a corner has too small a radius, cracks may occur due to changing thermal stresses.
In contrast to the die casting molds, continuous casting molds generally consist of copper plates which have water cooling for better heat dissipation. Compared to steel, copper is distinguished by very good thermal conductivity and thus enables rapid and efficient solidification of the melt.
The main products for continuous casting include slabs for sheet metal products. These are, in simplified terms, blocks of cast steel, aluminum or copper. These slabs are usually produced in the mold as a continuous strand and can be rolled out to form sheets during further processing in rolling mills.
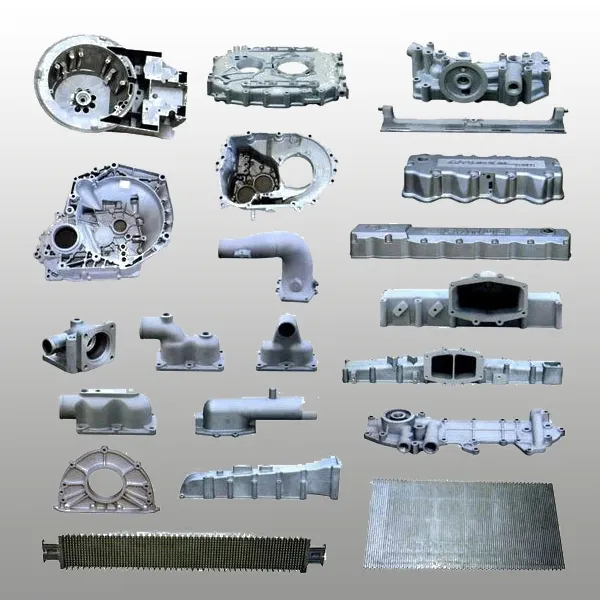
Main Technologies Co., Ltd.
The use of molds makes it possible to achieve several advantages, for example compared to sand casting. This includes:
- Low space requirement compared to sand casting
- Permanent form, therefore reusable
- High surface quality by finishing
- High casting power
- High degree of automation
- Low wall thicknesses
Casting materials for molds
The molds are suitable for the processing of numerous materials, the difference in melting point between the mold material and the casting material being taken into account. The typical cast materials include:
- Steel
- brass
- Cast iron
- Aluminium
- zinc
- Silicon tombac
Find companies for molds
Cokillen can be found most easily through Techpilot, Europe's largest platform for drawing parts in Europe. The application offers an excellent way to find new suppliers and write out parts. Over 24,000 companies are registered with Techpilot and looking for jobs.
As a buyer, you can use the full functionality of Techpilot free of charge. This includes, in particular, creating requests for parts. Interested contractors will send you concrete offers that you can compare with price, quality and delivery time. This saves you an elaborate and time-consuming supplier search.
Techpilot staff have a wide range of expertise in the industry and help you with advice and action. The telephone service is also free of charge and is extremely helpful in creating inquiries.
Techpilot is Europe’s largest platform for the manufacturing industry.
For over 25 years, we’ve been connecting buyers, suppliers, and manufacturers that are the perfect match – enabling accurate price discovery for custom-made parts. Covering the full spectrum of mechanical components and supporting more than 280 manufacturing technologies, Techpilot is the market leader in Europe.Buyers gain instant access to qualified suppliers, full market transparency, and increased efficiency in their e-sourcing processes.
Suppliers benefit from high online visibility, extended media reach, and a profitable digital sales channel through Techpilot.
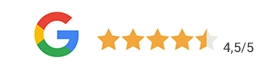
Lexicon Themes
- Metalworking (31)
- Plastic processing (8)
- Parts (8)
- Surface treatment (8)
- Welding (7)
- Machining (6)
- Sheet metal processing (6)
- Cutting (6)
- Turning (5)
- Manufacturing (5)
- Milling (4)
- Tool making (4)
- Suppliers (4)
- Casting (4)
- Procurement (4)
- Contract manufacturing (3)
- Profiles (3)
- Automation technology (2)
- Gearing & Thread (1)
- Forging (1)
- Wire processing (1)
- Heat treatment (1)