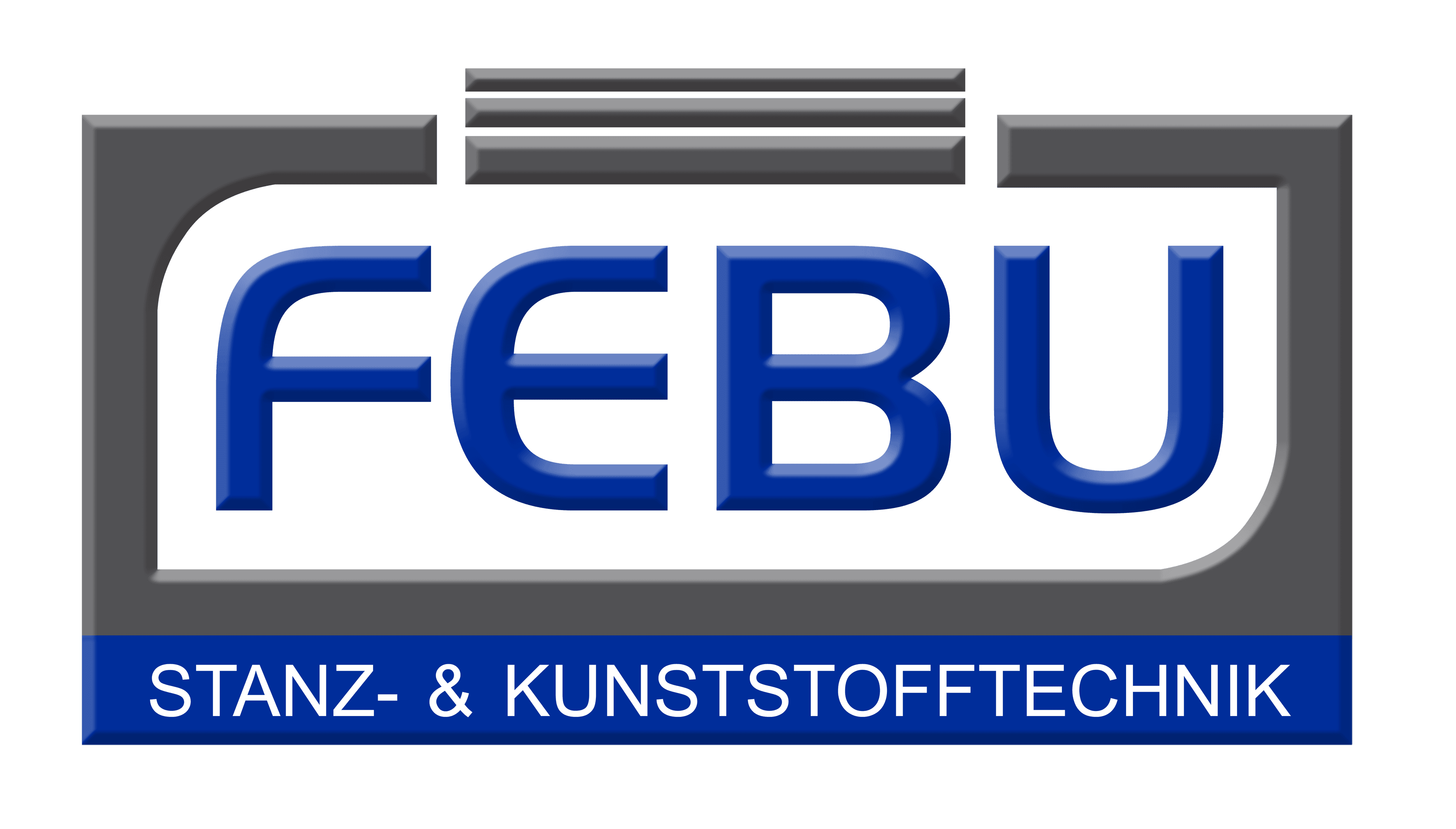
Febu GmbH
Contacts
Henrik Fey
Technical management
Phone:
E-Mail:
Competencies
Parts (3)
Technologies
Injection Moulding, Extruding
Technologies | Lotsize | Length | Width | Height | Diameter | Weight | Material thickness |
---|---|---|---|---|---|---|---|
Injection moulding | 1 - 99999998 | max. 500 | max. 500 | max. 500 | - | max. 0.72 | - |
Injection-mould around inserts | 100 - 10000000 | 1 - 300 | 1 - 300 | 1 - 300 | - | max. 0.5 | - |
Multi component injection moulding | 100 - 10000000 | 1 - 300 | 1 - 300 | 1 - 300 | - | max. 0.5 | - |
Company description
We, the FEBU are a medium-sized company with 29 employees, and headquarters in the industrial area of Burbach – Würgendorf, plant road 19, with direct connection to the A45. The foundation of the company FEBU dates back to 1965. At that time the father of the current managing director Andreas Fey started with the production of punching, pressing and drawing tools, as well as with the production of windshield washers made of metal, in the rooms of his parents’ house. Due to the increasing demand, the constantly growing space requirements were initially met with the construction of a 150 m² production and storage hall in Burbach-Holzhausen in 1970. Due to the further steady growth of the company, the production and storage areas were moved to Burbach-Würgendorf in 1988, not least because of the favourable transport connections. Through expansions in recent years, a total of 5,350 m² of production and storage space is currently available. In the following years the product range was extended in all areas. Stamping technology With the founding of the company in 1965, the production of the first stampings for the company’s own windscreen washers and water slides began. In addition to the production of stampings for the company’s own products, other customers were quickly acquired and sales were continuously increased through constant investment in the latest machines. Thus, the most modern automatic punching machines and eccentric presses up to 200t pressure are available. For further processing, we have welding presses, automatic threading machines, as well as stud welding equipment and various special machines. Here a production can take place on tools manufactured by us or provided by you. Among steel (blank, galvanized + coated) and stainless steel we also process non-ferrous metals. Injection moulding technology With the decision of the current managing director Andreas Fey in 1993 to implement the production of plastic injection molded parts for the ice scrapers and windshield washers in house to be able to react faster and more flexibly to customer requests, he laid the foundation for the current 16 machines comprehensive injection molding production. After the purchase of the first injection moulding machine it did not take long until further articles from other areas were added and the first 2-component injection moulding machine was purchased, first for the production of the first own 2-component ice scraper, later also for further customer-specific articles. Gradually, the injection moulding production was expanded and finally, with the takeover of the company Schmidt Kunststofftechnik (founded in 1955) at the Biedenkopf-Eckelshausen location in April 2020, a second location was added. Toolmaking The in-house tool shop, with which the then founder of the company Horst Fey laid the foundation stone, is still the pillar of all production areas today. Thanks to our ultra-modern tool shop, we can react quickly and precisely to customer requirements and maintain our tools accordingly. Here we design and manufacture punching and injection moulding tools with a tool length of up to 2,000 mm, as well as fixtures and mountings for various machines. Cleaning equipment and ice scrapers The production of cleaning equipment includes the production of metal windscreen washers and water sliders, as well as the production of various plastic windscreen washers and ice scrapers. By investing in the most modern machines and developing our own products and tools, we are still able to produce competitively in this field. Since its foundation in 1965, FEBU has been able to establish itself throughout Europe. The export, also beyond the European borders, shows positive figures. Due to a manageable number of employees the company remains flexible and can react quickly to special customer requirements.
Copmany images
Materials
Heavy metals
Copper-zinc alloys (brass)
Copper and copper alloys
Zinc and zinc alloys
Solder
Light metals
Aluminium and aluminium alloys
Magnesium and magnesium alloys
Titanium and titanium alloys
Steel
Structural steel
Case hardening/tempering steel
Stainless steel (rust-proof V2A)
Stainless steel (rust-proof V4A)
Free-cutting/mild steel
Tool steel
Spring steel
Cold extruding steel
Plastics/synthetic materials
Thermoplastics
Acrylic (PMMA)
High performance plastic
Thermosets
Elastomers
Silocone (LSR)
Natural and vulcanised rubber
Glass fibre-reinforced plastic
Carbon fibre-reinforced plastic
Particle reinforced composite materials
Wood-Plastic-Composites (WPC)
Natural Fibre Composites (NFC)
Non-metal inorganic materials
Graphite
Are you a supplier?
Find perfectly matching requests.
Are you a buyer?
Submit your request.