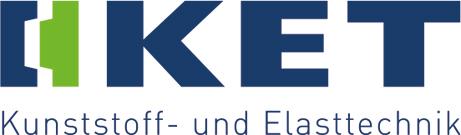
KET Kunststoff- und Elasttechnik GmbH
Contacts
Christopher Banks
Marketing and Sales
Phone:
E-Mail:
Janis Hildebrand
Technical management
Phone:
E-Mail:
Rosalie Klose
Marketing and Sales
Phone:
E-Mail:
Competencies
Parts (1)
Technologies
Injection Moulding, Extruding
Technologies | Lotsize | Length | Width | Height | Diameter | Weight | Material thickness |
---|---|---|---|---|---|---|---|
Injection moulding | 1 - 1000000 | 20 - 500 | 5 - 500 | 10 - 500 | - | max. 4 | - |
Extrusion (profile) | 1 - 60000 | - | 5 - 50 | 5 - 50 | - | - | - |
Injection-mould around inserts | 1 - 1000000 | 5 - 500 | 5 - 500 | 5 - 500 | - | max. 4 | - |
Multi component injection moulding | 1 - 60000 | 3 - 300 | 3 - 300 | 3 - 300 | - | max. 4 | - |
Transfer moulding | 1 - 1000000 | 5 - 300 | 5 - 300 | 5 - 300 | - | max. 4 | - |
Extrusion blow moulding | 1 - 60000 | 20 - 350 | 5 - 350 | 20 - 350 | - | - | - |
Compression moulding | 1 - 60000 | 5 - 1200 | 5 - 1000 | 5 - 300 | - | max. 4 | - |
Company description
Liegau-Augustusbad is located in the vicinity of Dresden/Saxony, with perfect logistical connections to the motorway and Dresden airport. The Company’s manufacturing area is around 26,000 square metres and has been producing a wide range of moulded rubber components since the early 1900s. As a result, we have gained extensive knowledge in the field of rubber processing and parts manufacturing. Due to the fall of the DDR, the Company was later privatised in 1991, with large investments made in a more modern manufacturing process and extension of the machine park. The KET has currently around 50 highly skilled and motivated employees, enabling us to work a 3 shift system in order to fulfil our customer’s needs, whether it’s a Simple form or a complicated Moulding, we aim to please. Through our quality management system DIN EN ISO 9001 and DIN ISO 13485 certification. We are able to guarantee a very high level of customer satisfaction and quality of our products. Our technology department control and monitor the preparation, introduction and implementation of our production processes according to clearly defined specifications. The most important operating procedures we use within our production processes are: • 3-D-printing/Plotting • compression moulding process (CM) • transfer moulding process (TM) • injection moulding process (IM) • injection transfer moulding process (ITM) The vulcanisation operating processes are carried out in semi and/or fully automatic machining cycles. We also offer a number of procedures and technologies for the post-treatment of produced products (finishing): • thermal post-treatment (Curing) • mechanical post-treatment (low-temperature deburring) • manual post-treatment (hand deburring / assembly) • covering and coating processes We manufacture parts from rubber compounds such as EPDM, NBR, SBR, CR, ACM, NR, FPM, IIR, MVQ and LSR (silicones). All of which have received clearance from the automotive industry, as well as KTW and DVGE clearance for the food and pharmaceutical industries. In addition to rubber vulcanisation, we also manufacture a large quantity of thermoplastic elastomers (TPE). Another key feature of the materials sector is the use and manufacture of recycled rubber granulates from various basic elastomers The equipment and control systems of our Machine Park reflect the current state of the art in engineering, thus Enabling us to meet the future requirements of production engineering. We can manufacture parts from less than 1 Gramm up to 4,5 Kilograms.
Machines (4)
Copmany images
Materials
Plastics/synthetic materials
Thermoplastics
High performance plastic
Thermosets
Elastomers
Silocone (LSR)
Natural and vulcanised rubber
Glass fibre-reinforced plastic
Industries
Plant engineering and construction
Boiler, container and tank construction
Air conditioning, refrigeration and ventilation industry
Power generation and transmission industry
Electrical industry
Automotive and vehicle construction
Household appliance industry
Railway and rail vehicles industry
Clean room technology
Medical technology
Mining and tunnel engineering
Hydraulic and pneumatic industry
Special purpose machinery manufacturing
Are you a supplier?
Find perfectly matching requests.
Are you a buyer?
Submit your request.