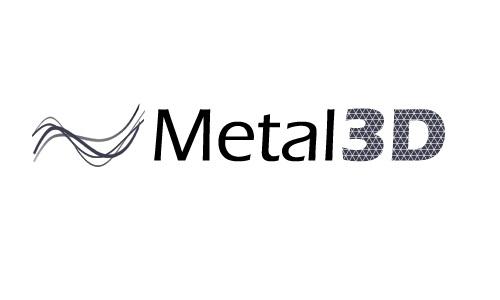
Metal3D SA
Contacts
Nikolaos Efentakis
Owner, company manager, member of the board
Phone:
E-Mail:
Competencies
Parts (1)
Technologies
Additive Manufacturing
Technologies | Lotsize | Length | Width | Height | Diameter | Weight | Material thickness |
---|---|---|---|---|---|---|---|
Fused deposition modelling (FDM) | 1 - 1000 | 5 - 200 | 5 - 250 | 5 - 200 | - | - | - |
3D printing (general) | 1 - 2000 | 6 - 150 | 6 - 250 | 6 - 155 | - | - | - |
Company description
Metal3D SA Has been established in order to become a key player on the fast developing market of the 3D metal printing. Metal3D SA is a valuable partner for any company wishes to benefit from this innovative technology, by offering engineering and manufacturing services. We are aware that obtaining a state-of-the-art technology doesn’t end with equipment delivery. In itself, equipment doesn’t generate new competences. The real challenge is to develop the skills and knowledge to fit this innovative process into the current market needs. Not only to target in engineering, aiming on “how a metal part should be printed”, but to optimally combine 3D printing with the traditional manufacturing technologies to generate the maximum benefit. Metal 3D Printing Equipment We had carefully analyzed the currently available technologies in this field and we had chosen to invest in this very first step in the Studio System+ from Desktop Metal Inc. and the Bound Metal Deposition (BMD®) technology. BMD is the newest, but also the most mature technology in this field. BMD substantially relies on MIM (Metal Injection Molding), a mature and proven production technology for metal parts. MIM produces metal components in three steps. Initially a mixture of metal powder with a thermoplastic binder is injected in a mold in a process similar to injection molding. From this stage we get the so called “green body” of the part. In a subsequent step, the binder is removed from the “green body”, leading to a brittle part known as “brown body”. Finally the “brown body” is sintered and the final sound metal part is produced. BMD follows also these three stages with only a major difference on the first stage. The “green body”, instead of being molded, it is built by a 3D printer, which is similar to the FDM plastic 3D printers. Raw material has not the form of filament, but of rods made of a thermoplastic binder with a high concentration of metal. Metal3D SA Services We provide a complete range of services in the field of custom metal 3d printing. To do so, we assist our customers in the first and most important question: “Will it be of any benefit to 3D print a metal part compared to the traditional manufacturing operations?” In detail, we offer: 1. 3D printing of metal components as a service, including engineering consultancy for the adaptation of the part design on the specific requirements of this new production method 2. A wide range of post printing operations, i.e. high precision CNC machining, surface treatments, thermal treatments etc. 3. Metal 3D printing of cavity inserts for the construction of low volume injection molds and production of the plastic moldings. 4. Functional assemblies comprised by metal (3D printed or/and machined) components, plastics (molded or 3D printed) and standard items. 3D Printing Metals We currently have experience with two materials: • 17-4PH (EN 1.4542). A versatile stainless steel featuring substantial mechanical properties (ultimate tensile strength 1042MPa) and hardness (HRC 37). 17-4PH can be furthermore hardened (up to 48HRC) and also plasma nitriding. 17-4PH meets a 98% density after sintering • 316L. Characterized by its corrosion resistance and performance at both high and low temperatures, 316L is a fully austenitic stainless steel. It is used often in applications involving chemical processing, salt water environments, and household or industrial fixtures. Before the end of 2019 we will start using also H13, as soon as it is released from Desktop Metal. H13 is a chromium hot-work steel, which is widely used in hot and cold work tooling applications. Due to its excellent combination of high toughness and fatigue resistance. H13 is used more than any other tool steel in tooling applications. Desktop Metal plans to release also the following materials: Alloy 625, AISI 4140, and Copper.
Machines (3)
Copmany images
Materials
Plastics/synthetic materials
Thermoplastics
Acrylic (PMMA)
High performance plastic
Thermosets
Elastomers
Silocone (LSR)
Natural and vulcanised rubber
Glass fibre-reinforced plastic
Carbon fibre-reinforced plastic
Particle reinforced composite materials
Wood-Plastic-Composites (WPC)
Natural Fibre Composites (NFC)
Sintered materials
Metal powder for formed parts
Metal powder for hard metal
Heavy metals
Copper-zinc alloys (brass)
Copper and copper alloys
Zinc and zinc alloys
Solder
Light metals
Aluminium and aluminium alloys
Magnesium and magnesium alloys
Titanium and titanium alloys
Steel
Structural steel
Case hardening/tempering steel
Stainless steel (rust-proof V2A)
Stainless steel (rust-proof V4A)
Free-cutting/mild steel
Tool steel
Spring steel
Cold extruding steel
Are you a supplier?
Find perfectly matching requests.
Are you a buyer?
Submit your request.