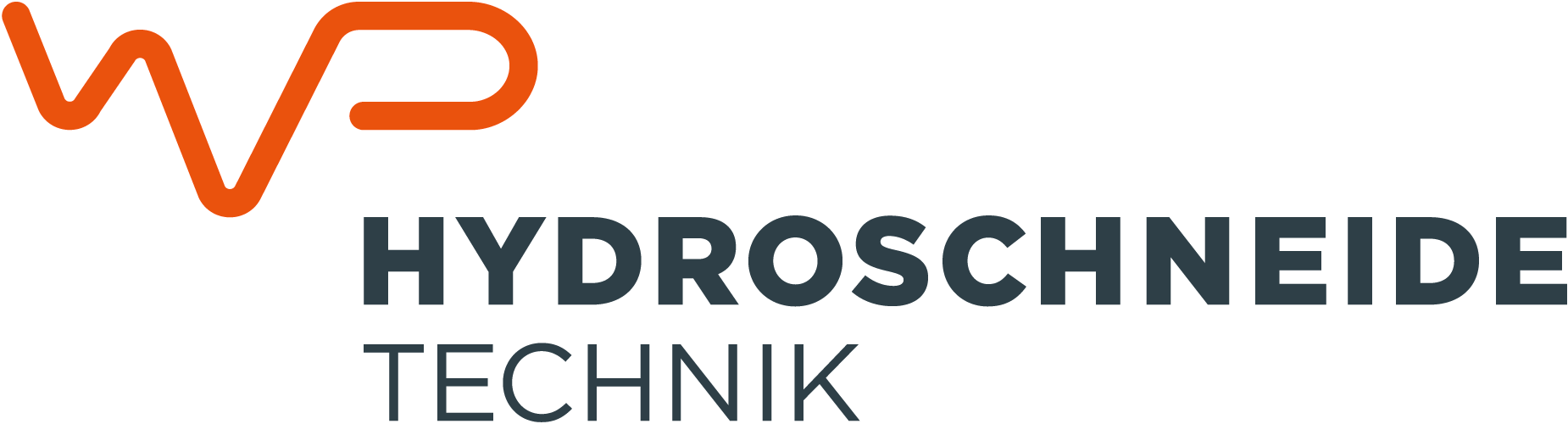
W.P. HydroschneideTechnik GmbH & Co. KG
Contacts
Michael Meßmer
Marketing and Sales
Phone:
E-Mail:
Competencies
Technologies
Water jet cutting
Technologies | Lotsize | Length | Width | Height | Diameter | Weight | Material thickness |
---|---|---|---|---|---|---|---|
Water jet cutting 2D | 1 - 100000 | 12 - 3000 | 10 - 2000 | - | - | max. 1500 | 0.1 - 150 |
Water jet cutting 3D | 1 - 50000 | 12 - 3000 | 10 - 2000 | 0.5 - 650 | - | max. 1500 | 0.5 - 1001 |
Water jet cutting, tube & section | 1 - 50000 | 12 - 3000 | 10 - 2000 | 1 - 650 | 5 - 650 | max. 1500 | 0.5 - 1001 |
Company description
The technical capabilities of the WP hydraulic cutting technology: • Water jet cutting in 2-D (Including systems with up to 6000 bar and angle correction) • Water jet cutting in 3-D • Prototype • Custom • Design and construction of devices • Preparation and processing of CAD data What materials we can edit? • Rubber profiles • Plastics • Foam • foam rubber • Aluminium • Steel • Stainless steel • Titanium • Copper • CFRP • GRP • Marble • Stone • Acrylic • Glass • Special materials • and much more What are the advantages of water jet cutting? • Materials can, in contrast to all other separation methods to a thickness of 100 - 150 mm are processed • Cost-effective low-volume or prototype production • Economical separation process (no tool change, simple devices, no clamping devices) • Low program creation time • Cold cutting process (no thermal and chemical changes / change in the microstructure of the material, thus no material distortion) • Multiple operations (suchAs notches, holes, figure and contour) can be cut in one step • Scratch-free processing of the surface • No generation of toxic gases or vapors • no development of dust, chips or smoke • environmentally friendly separation methods (the use of natural substances such as water and sand) • high precision • No part warpage (except where appropriate material residual stress) • Processing option for (almost) all materials (even wrmeleitende or reflective materials) • Good cutting ability for composite and fiber-reinforced materials, suchB. sandwich materials such as CFRP or GFRP • No deformation of the material by pressure in the cutting area (only one cutting pressure of approximately 40 N on the workpiece) • No violation of the material surface (no hairline cracks in the cutting area) • Complex shapes are cut with high precision • clean cut edges without fraying and only with minimal burr • Filigree cut designs with fine contours and minimum bridge widths are technically feasible • Low material loss and waste (less kerf and optimizing material utilization) • Small cutting gap (in clean water 0.06 to 0.3 mm, using abrasive from 0.76 to 1.2 mm) • Cutting of any possibility, even complex contours and shapes, sharp angles, oblique cut edges and small inner radii • cutting ability in all directions • section may use or end at any point of the workpiece What speaks for the WP Hydroschneide technology
Copmany images
Materials
Steel
Structural steel
Case hardening/tempering steel
Stainless steel (rust-proof V2A)
Stainless steel (rust-proof V4A)
Free-cutting/mild steel
Tool steel
Spring steel
Cold extruding steel
Advanced Materials
Nickel alloy (Inconel, Monel, Hastelloy)
Carbide
Sintered materials
Metal powder for formed parts
Metal powder for hard metal
Cast metals
Cast steel
Cast iron
Heavy metals
Copper-zinc alloys (brass)
Copper and copper alloys
Zinc and zinc alloys
Solder
Light metals
Aluminium and aluminium alloys
Magnesium and magnesium alloys
Titanium and titanium alloys
Non-metal inorganic materials
Ceramics
Glass
Concrete
Cast minerals
Graphite
Natural materials
Wood/timber
Rock
Plastics/synthetic materials
Thermoplastics
High performance plastic
Thermosets
Elastomers
Silocone (LSR)
Natural and vulcanised rubber
Glass fibre-reinforced plastic
Carbon fibre-reinforced plastic
Particle reinforced composite materials
Wood-Plastic-Composites (WPC)
Natural Fibre Composites (NFC)
Industries
Electrical industry
Machine tool manufacturing
Medical technology
Fittings engineering
Special purpose machinery manufacturing
Boiler, container and tank construction
Precision engineering, mechatronics and optics
Power generation and transmission industry
Chemical industry
Plant engineering and construction
Automation and control engineering
Mining and tunnel engineering
Air conditioning, refrigeration and ventilation industry
Aerospace and aviation industry
Telecommunication industry
Packaging industry
Measurement and control technique, laboratory equipment
Shipbuilding industry
Automotive and vehicle construction
Building, agricultural and forestry machinery manufacturing
Paper and printing machinery industry
Lighting industry
Clean room technology
Drive and gear engineering
Railway and rail vehicles industry
Hydraulic and pneumatic industry
Construction and architectural supplies
Apparatus engineering
Office machinery and supplies
Furniture industry
Mechanical engineering
Military engineering
Are you a supplier?
Find perfectly matching requests.
Are you a buyer?
Submit your request.